Tra i tanti obiettivi della progettazione di un componente, nella maggior parte dei casi è necessario che esso non si rompa durante l’esercizio, o che lo faccia dopo aver compiuto un numero prestabilito di cicli di lavoro. Alcuni componenti invece necessitano di una progettazione mirata a studiarne il tipo di rottura, la velocità di deformazione e l’energia assorbita. È questo il caso della struttura di assorbimento per gli impatti frontali dei prototipi di Formula Student. Essa è vincolata da numerose regole che ne limitano i materiali e le geometrie adottabili. Inoltre, descrivono la procedura da utilizzare per il test di impatto dinamico in caso di progettazione con materiali non standard. La prova consiste in un drop test, ovvero un test in cui viene fatta impattare una massa in caduta libera sull’oggetto in esame.
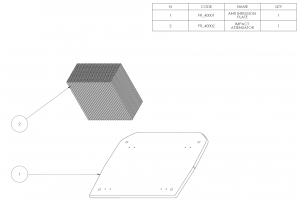
La struttura protagonista del test di Dynamis PRC è composta da un supporto che simula il telaio della vettura e, imbullonato al supporto, dall’assieme che assorbe gli impatti frontali. Quest’ultimo è formato da due componenti: l’attenuatore di impatto e il pannello anti-intrusione. Il primo ha la funzione di assorbire l’energia cinetica della massa in caduta libera, attenuando la decelerazione e riducendo il picco massimo di forza che il veicolo subisce. Il secondo invece ha la funzione di supportare l’attenuatore e in caso di incidenti evita che eventuali detriti provenienti dal fronte della vettura o corpi estranei possano penetrare nell’abitacolo e quindi colpire il pilota. Lo scopo del test è misurare
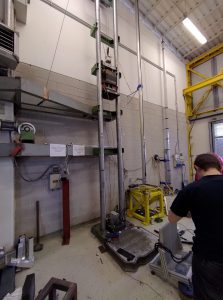
l’energia assorbita dalla struttura, le decelerazioni media e massima raggiunte, la deformazione massima subita dal pannello anti-intrusione e il picco di forza. È fondamentale contenere i valori di questi parametri, in modo tale che il pilota non sia soggetto a decelerazioni, e quindi forze, eccessive in caso di incidente, garantendo la sua incolumità.
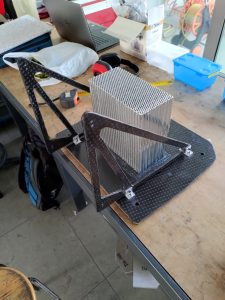
Nel drop test sono inclusi anche i supporti dell’alettone anteriore, che vanno inseriti nella prova per l’omologazione finale dell’assieme in quanto influenzano forze e decelerazioni complessive.
Impatti e sicurezza
Dalla stagione 2020, in caso di utilizzo di materiali compositi per il pannello anti-intrusione, il regolamento prevede che il supporto debba essere realizzato con il medesimo materiale del telaio, quindi in questo caso in materiale composito. È obbligatorio produrlo con la medesima sequenza di laminazione e identici core, sia
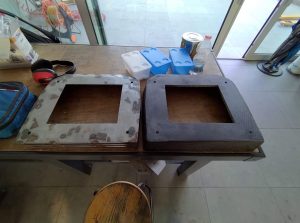
come materiali che come spessore. La prima parte dello studio del nuovo piatto anti-intrusione ha riguardato proprio la simulazione della struttura di supporto, per individuare l’altezza della sezione di appoggio e fare in modo che il supporto non cedesse durante il test.
Riguardo alla struttura di assorbimento che viene montata sulla vettura, i progettisti del DynamiΣ PRC, dopo svariate stagioni di sperimentazione, hanno optato per l’utilizzo di un attenuatore formato da un unico pezzo di honeycomb di alluminio: rispetto alle versioni precedenti assorbe una maggiore quantità di energia, pur rispettando le dimensioni minime imposte dal regolamento. Per quanto riguarda invece il pannello anti-intrusione, con la progressiva evoluzione del prototipo ci sono stati notevoli miglioramenti dal punto di vista dei materiali utilizzati e quindi della massa finale: esso viene prodotto con struttura sandwich, formata da due lamine di materiale composito a matrice epossidica rinforzata con fibra di carbonio e core alveolare.
Per lo sviluppo della versione più aggiornata del pannello, gli ingegneri hanno inizialmente analizzato nel dettaglio i dati del test precedente per ricreare la condizione di carico adeguata da applicarvi. Una volta scelti il tipo di carico e la sua intensità, sono state testate diverse sequenze di laminazione, variando sia il numero di pelli sia la loro orientazione nel piano. È di cruciale importanza scegliere la giusta orientazione dei diversi layer di fibra di carbonio, per poter coniugare tra loro aspetti come rigidezza, capacità di assorbimento dell’energia e limitare la deformazione massima in seguito al test.
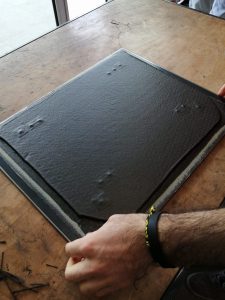
Una volta individuato il layup più promettente, i progettisti hanno simulato l’utilizzo di core di differenti spessori, per verificare se si potesse ridurre l’ingombro longitudinale utilizzando spessori minori per il core, oppure ridurre il numero di layer di fibra di carbonio, e quindi ridurre notevolmente la massa del pannello, grazie all’utilizzo di core più spessi.
La versione finale sfrutta un leggero incremento dello spessore del core di 2 mm rispetto alla versione precedente, che permette di ridurre il numero complessivo di layer da 16 a 12, riducendo la massa complessiva del pannello del 20%. La rigidezza data da un core più spesso aumenta notevolmente il momento di inerzia del pannello, e quindi la sua rigidezza complessiva. Questo permette di ottenere lo stesso valore di rigidezza utilizzando un minor numero di pelli. Siccome la densità del composito è notevolmente maggiore rispetto alla densità del core alveolare utilizzato, l’aumento di spessore del pannello è giustificato dalla riduzione della sua massa.
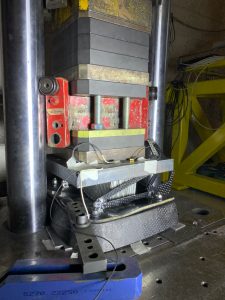
Il nuovo assieme ha superato il test rispettando tutti i parametri richiesti dal regolamento
in termini di energia assorbita, accelerazioni, forze generate e integrità del piatto anti intrusione, e verrà quindi utilizzato sul prototipo della stagione 2021, che attualmente è in fase di assemblaggio.
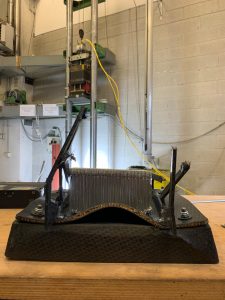
Futuri sviluppi riguarderanno la sostituzione
dell’assorbitore in honeycomb di alluminio con una struttura composita realizzata in fibra di carbonio, che permetterà un’ulteriore riduzione della massa complessiva dell’assieme.
di Jacopo Muzio